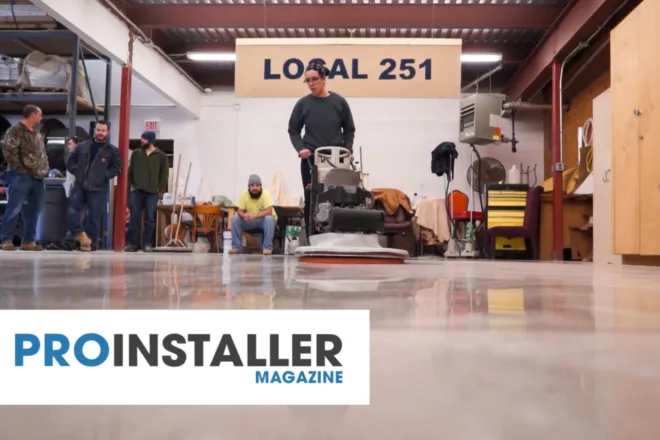
*This article by INSTALL executive director David Gross was originally featured in the May/June 2024 edition of ProInstaller Magazine.
Concrete Polishing: Training Makes Work Shine in Competitive Space
By David Gross
The non-residential polished concrete market grew to over $1 billion in 2021, according to a report from Global Market Insights, and it’s predicted to continue growing at a rate of 4% over the next few years. For flooring contractors, that means greater demand for concrete polishing expertise and more opportunities to win these types of projects.
While some flooring contractors are jumping into concrete polishing to take advantage of this growth, it’s the contractors who can demonstrate their expertise with training and certification credentials who have the clear advantage. With large commercial and industrial projects accompanied by equally large price tags and investment risks, architects and specifiers are more cautious than ever when choosing contractors to perform concrete polishing work. To make the short list of highly qualified contractors for jobs like these, many flooring professionals are seeking training or certification from accredited organizations with a curriculum dedicated to concrete polishing. This training includes classroom instruction and hands-on practice with concrete polishing tools, equipment, techniques and products, giving contractors the advanced education and skills needed for a competitive edge.
For a glimpse into this training and the value it adds to a flooring business, here’s a look at a core topic included in concrete polishing training along with some of the costly missteps formal training teaches contractors to avoid.
Wet & Dry Polishing Techniques
When preparing for a concrete polishing project, part of the expertise provided by the contractor is choosing between wet and dry polishing to achieve the desired flooring result. This decision is important because it impacts many other aspects of the project, from the tools and equipment needed to the working conditions of the larger project.
When wet polishing concrete, contractors use water during the grinding phase to keep the slab surface lubricated. This technique controls silica dust in the work area by trapping the dust in water. Using water also lowers the amount of heat produced by grinding friction. Learning how to precisely control water and equipment during the process is vital for keeping the work area dust-free and allowing the grinding process to be most effective. The contractor must also know how to safely dispose of the resulting dust-and-water slurry generated during the grinding process and keep the surface clean between each step. Proper handling of the slurry is necessary for the safety of the work area and for readying the surface for subsequent processes. It’s also an observable aspect of professionalism often noticed by clients.
With dry polishing, the grinding equipment is outfitted with a dust collection system. This system, which typically includes a HEPA filter, protects the contractor and other site personnel from breathing hazardous silica dust particles. The dust collection system offers the advantage of keeping the work area clean as each pass is completed, differentiating it from wet polishing that requires more time for cleanup. Dry polishing provides the contractor and the client with the benefit of seeing the surface as work progresses, instead of having to wait for a wet surface to dry. Like wet grinding, the contractor must possess expertise in technique and equipment control, and carefully collect and dispose of the dust to keep the work area safe and create exemplary results.
Ultimately, neither polishing technique is easier than the other. Both require training and practice to properly handle and dispose of byproducts like slurry and dust to keep the worksite safe—and safety is just one aspect of the job. Surface preparation, tool and equipment use and maintenance, grit progression and product knowledge are also key factors in delivering professional-looking results.
The Risks of Inexperience
Concrete polishing is a complex process that demands precision, patience and deep material knowledge, and even the most experienced contractors can encounter conditions that adversely affect the quality of the finished floor.
To further illustrate the complexity of concrete polishing and emphasize why hands-on training is imperative, here are some examples of common missteps and their costly consequences.
Improper Surface Prep
Issue: Failing to properly prepare the concrete surface before beginning the polishing process. This includes not repairing cracks and not removing debris.
Impact: Leads to a poor-quality finish with visible imperfections and a high potential for rework.
Incorrect Grit Progression
Issue: Skipping grits or not using the correct sequence of abrasive pads during polishing. Untrained contractors may try to speed up the process by jumping from a coarse grit to a finer grit without the necessary grit progression in between.
Impact: Produces a floor that is improperly refined, shows scratches or does not achieve the desired polish level.
Use During Wet Grinding
Issue: Not using enough water during wet grinding or applying an uneven application of water across the concrete slab surface.
Impact: Can lead to uneven polishing, swirl marks and machine burn marks on the concrete surface due to insufficient lubrication and cooling.
Overworking the Concrete
Issue: Spending too much time polishing one area or using too much pressure. This is often due to inexperience with equipment or trying to correct an imperfection.
Impact: Causes dips and waves in the floor, making the surface uneven and negatively affecting gloss and reflectivity.
Glazing During Dry Polishing
Issue: Inexperienced contractors performing dry polishing are at greater risk of overworking the concrete surface, which can cause tools or equipment to overheat and, in worst cases, melt.
Impact: Costly damage to tools, equipment and the floor surface.
Improper Care of Equipment
Issue: Using equipment that has not been properly maintained, has dull grinding or polishing pads, or is performing poorly.
Impact: Reduces the efficiency of the polishing process, which can lengthen project time and lead to poor-quality finishes or damage to the concrete surface.
Ignoring Environmental Conditions
Issue: Not considering the temperature and humidity of the environment where the polishing is taking place.
Impact: Can affect how densifiers and sealants react and lead to a less durable finish.
Improper Use of Densifiers
Issue: Applying densifiers too early in the process or not allowing adequate time for the densifier to penetrate and react with the concrete.
Impact: Prevents the concrete from reaching its full hardness and durability, and affects the longevity and performance of the final polished surface.
Rushing the Process
Issue: Trying to complete the polishing process too quickly by rushing through the necessary polishing passes.
Impact: Compromises the quality and durability of the polish, leading to a finish that may not meet client expectations or performance standards.
Every step of the polishing process is an opportunity for mistakes when performed by an undertrained or inexperienced contractor, with the costly consequences of rework and disappointed clients. Formal training and certification minimize these risks, and their accompanying credentials help distinguish businesses in this competitive space.
Some Concrete Advice
Whether you want to expand your flooring business into concrete polishing or already have a concrete polishing business and want to win more work, professional training and certification can help. When choosing a training provider, look for an organization with a curriculum dedicated to concrete polishing led by technical experts and industry leaders in collaboration with product manufacturers. This will ensure the training represents current best practices, cutting-edge installation techniques and up-to-date product knowledge to help you take solid steps toward building success.
About the Author: David Gross is the executive director of INSTALL. Gross previously served as a full-time instructor for the Northeast Carpenter’s Apprenticeship Training Fund, achieving Advanced Instructor Certification through the UBC’s workforce development program. He holds a bachelor’s degree in economics, a Master of Business Administration, and is a Certified Safety Professional, as well as an Authorized OSHA Outreach Trainer and UBC Level III Instructor. He has served the United Brotherhood of Carpenters and Joiners of America (UBC) Local 251 Executive Board for almost 20 years, currently as vice president.